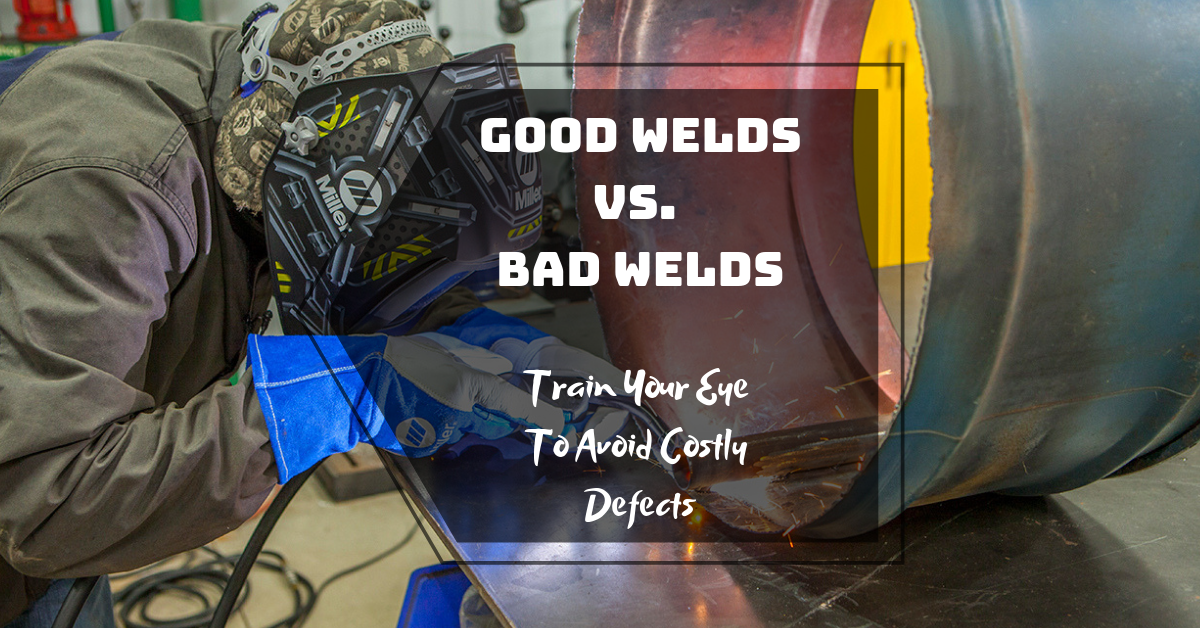
Good Welds Vs. Bad Welds Train Your Eye To Avoid Costly Defects Rate
A good weld will have a smooth, even bead. A bad weld will have a rough, uneven bead. Joint strength is how strong the joint is when the two pieces of metal are joined together by the weld. A good weld will have a strong joint that can withstand stress and vibration. A bad weld will have a weak joint that can break easily. What is a Bad Weld?

Bad Weld vs Good Weld, 1F Plate Stick Welding, SMAW Welding welder
Good MIG Welding: Stick Welding: Good TIG Welding Characteristics What Should a Good Weld Bead Look Like? What Degree of Weld Penetration is Good? What Does a Good Weld Sound Like? Bad Welds: What Does a Bad Weld Look Like? Examples of Bad Welds Bad MIG Welding: Poor Stick Welding: Bad TIG Welding: Preventing Bad Welds Concluding Considerations
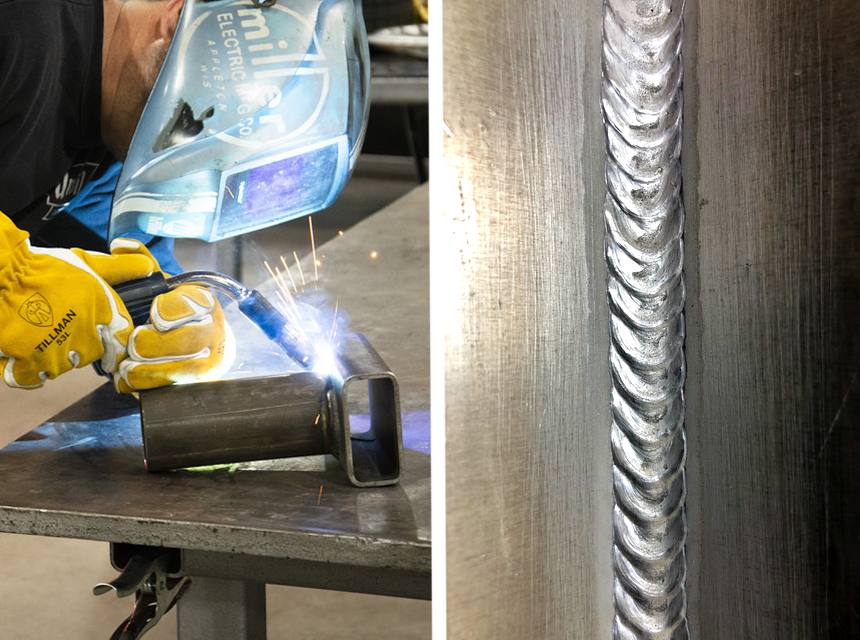
Good Weld vs Bad Weld 4 Methods for Proper Results and Testing Advice
Understanding Bad Welding vs. Good Welding. Quality of Fusion: Bad Welding: Bad welding often results in incomplete fusion, where the base metals fail to merge adequately. This lack of cohesion weakens the joint and compromises the overall strength of the structure. Incomplete fusion can lead to visible defects such as cracks and voids.
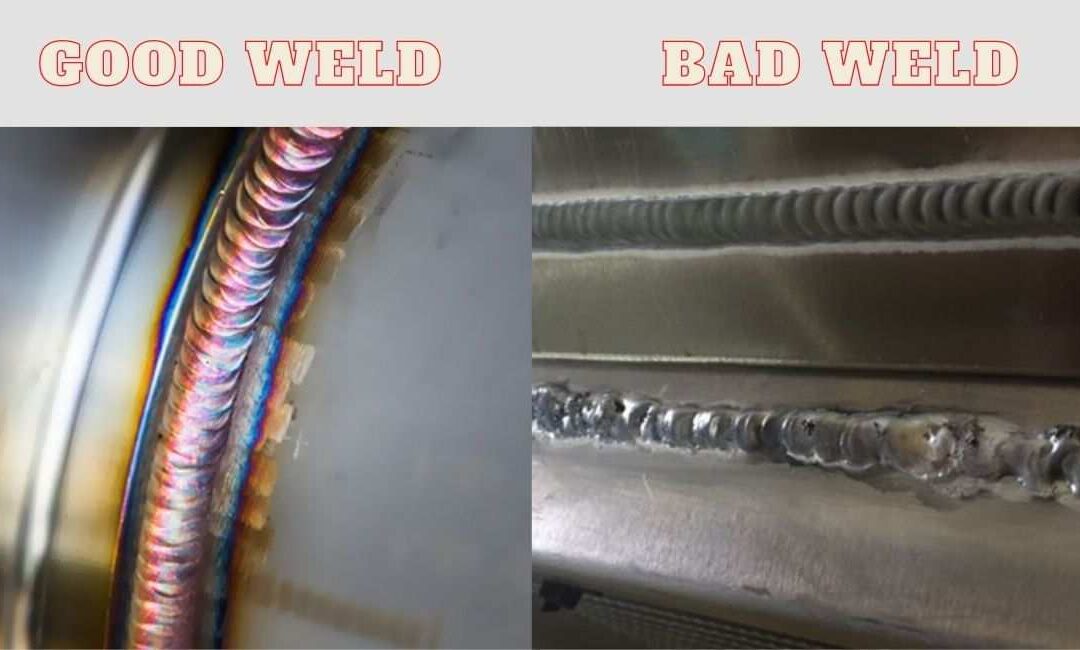
Good Weld Vs Bad Weld What's The Difference Between Them
This very skill of identifying good weld vs a bad weld is very valuable. This is particularly important if you are working in the food industry or any other industry which has high safety standards and quality regulations. Any guide won't help you, to magically become a professional welder.
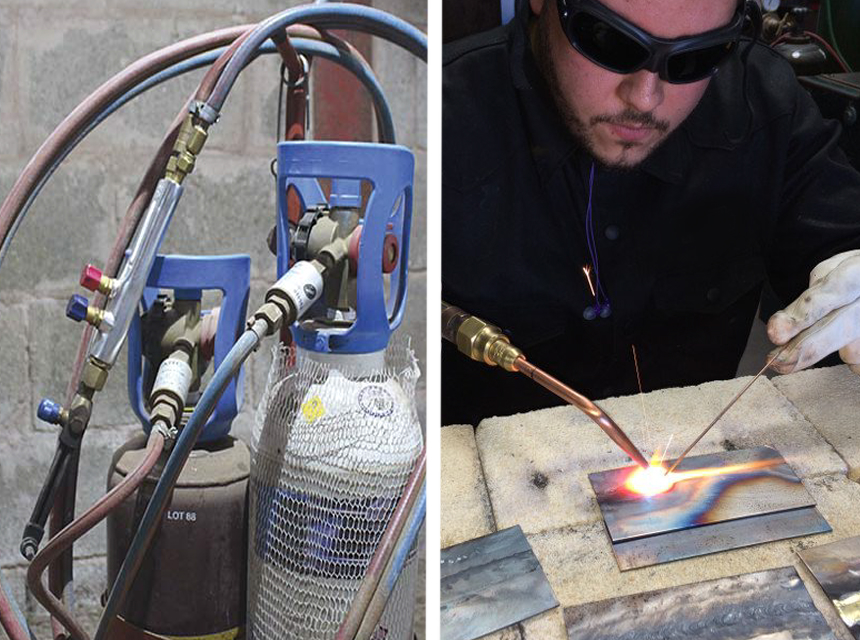
Good Weld vs Bad Weld 4 Methods for Proper Results and Testing Advice
When it comes to welding, there's good weld vs. bad weld. A good weld is essential if you want a strong product, and strong welds require a lot of skill. Having a welding certification will help you and your clients, but there are many ways to ruin a weld; bad equipment, bad setups, and even the wrong type of welding electrode can ruin a good weld.

Good Weld Vs Bad Weld Importance of Good Weld!
When you look at a good weld vs bad weld, you will notice five key differences that indicate poor quality. The weld joint will look messy. There may be uneven joints. A physical test may indicate weakness and movement. There may be jagged edges. There could be cracks in the joint. How Can You Tell the Quality of a Weld?
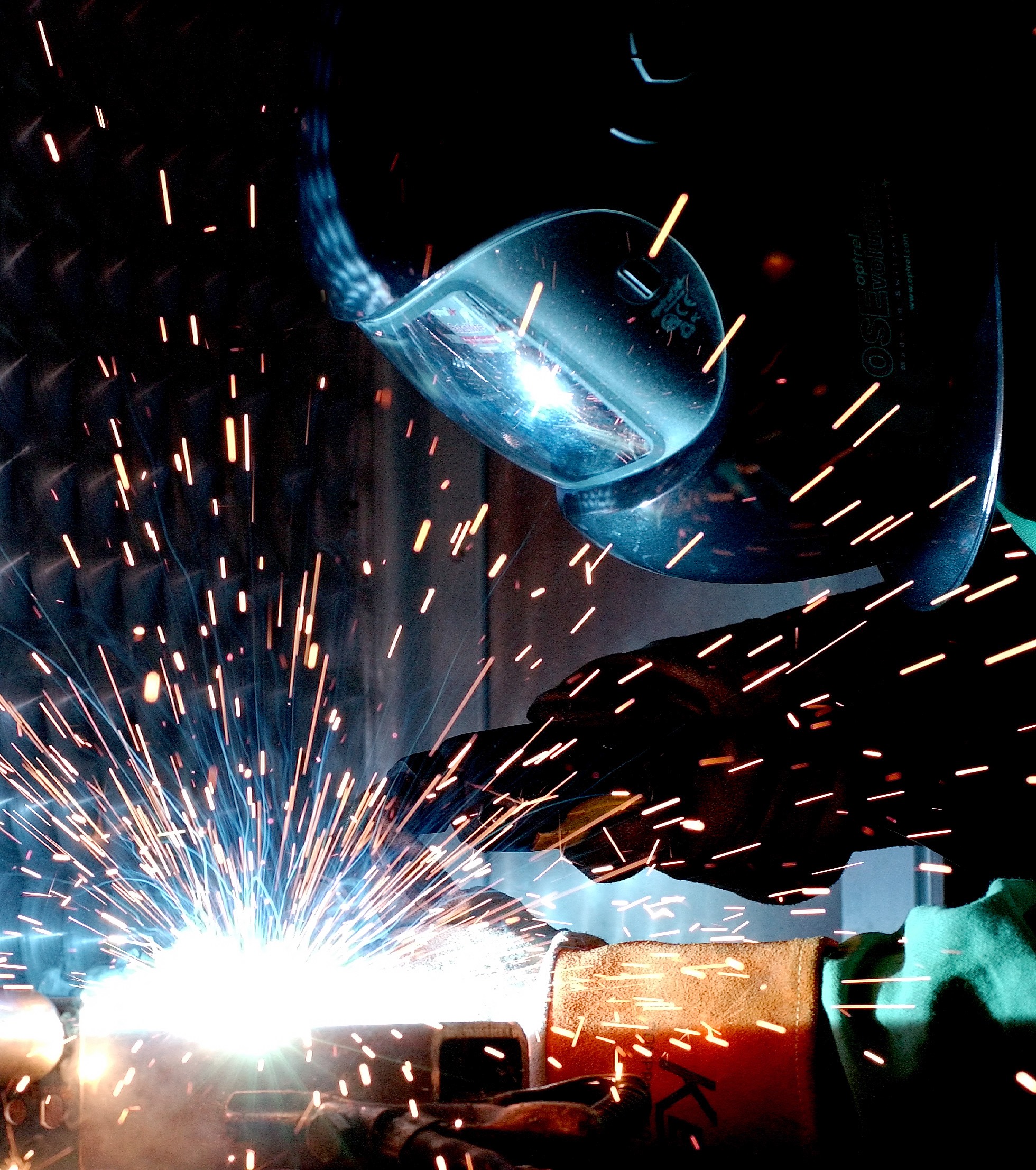
How to Spot A Good Weld vs Bad Weld
Several key aspects differentiate good welds from bad ones. Firstly, adequate penetration is essential. A well-executed weld means the filler metal has entirely fused with both base materials, providing the best joint strength and durability. Uniformity is also crucial, as it reflects proper heat distribution during welding.
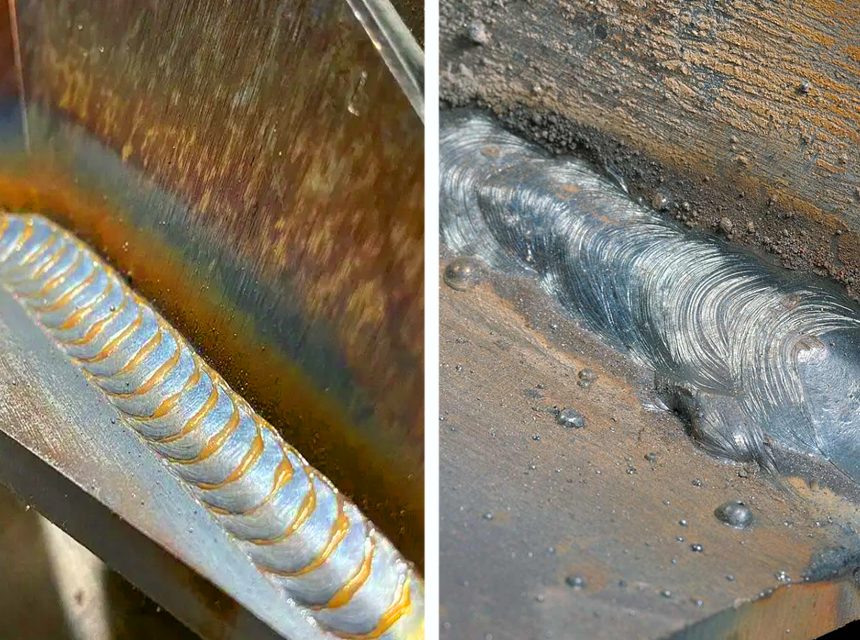
Good Weld vs. Bad Weld Everything You Need to Know ( Spring 2023)
Good and Bad Stick Weld Bead. The stick bad welds occur due to improper use of current, voltage, and travel speed. With the high amperage, you can't control the weld puddle that creates spatter whereas low amperage will stick the electrode while initiating the arc. Moreover, arc balancing is also important because a short arc keeps the.
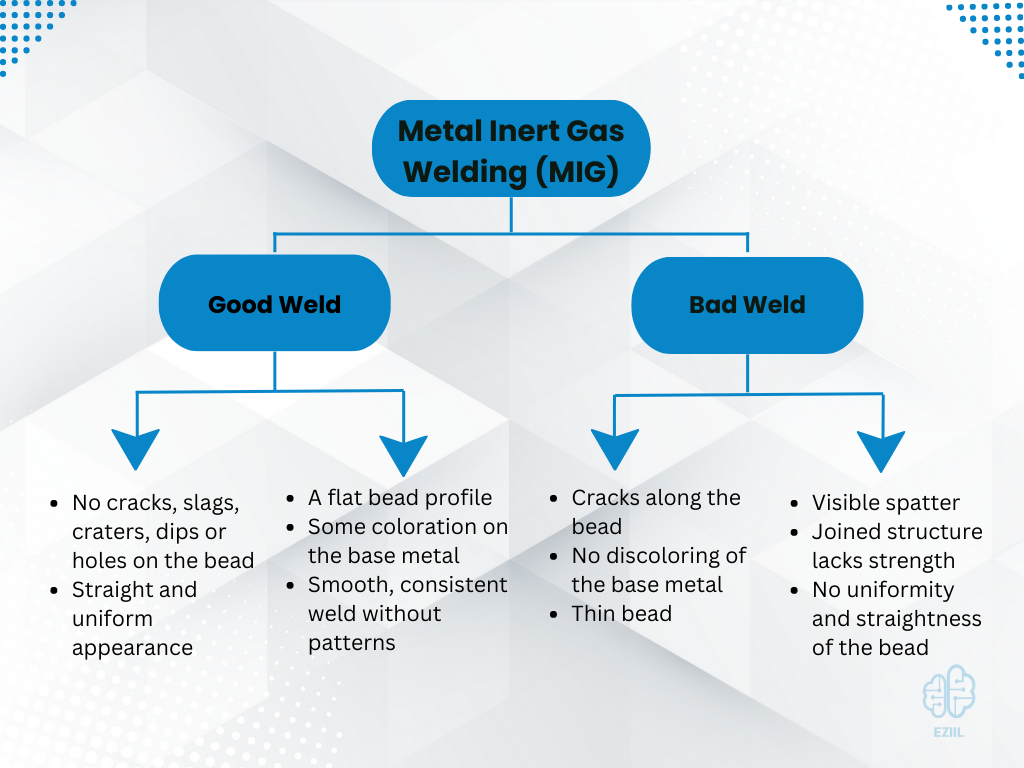
Good vs Bad Welds InDepth Examples and Images
2023-10-25 Welding is a process of joining two pieces of metal together by melting them with an electric arc or a gas flame. Welding is used in many industries, such as construction, manufacturing, automotive, aerospace, and more. However, not all welds are created equal. Some welds are good, while others are bad. How can you tell the difference?
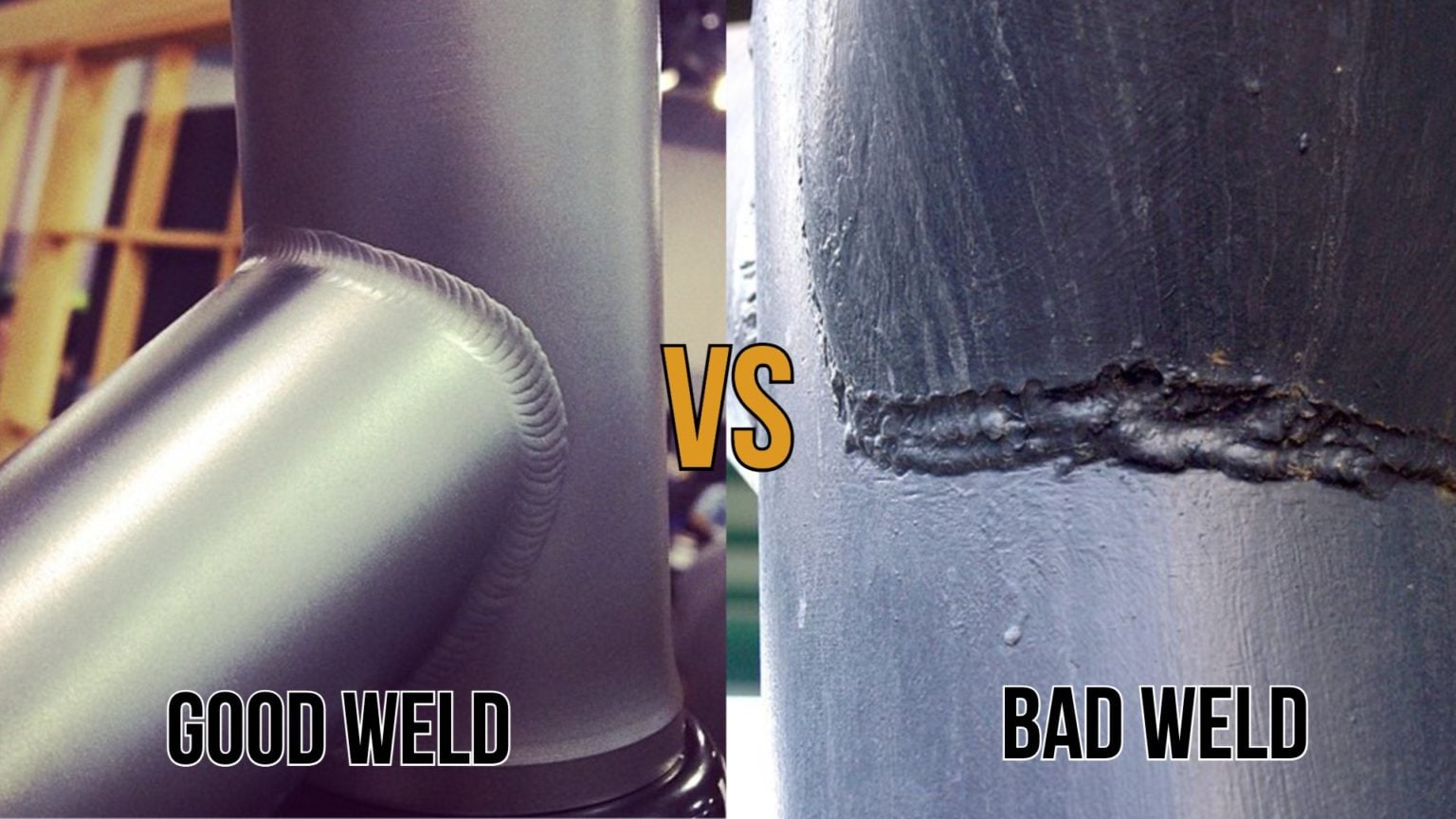
How to Identify a Good Weld vs Bad Weld (with Pictures) WaterWelders
Good Weld vs. Bad Weld First, What is a Bad Weld? Welding tasks involve base material, welding rods, welders, machines, auxiliaries' tools, and manual operation. Out of all these parameters, a Welder's Skill plays a decisive role to control the welding quality. Examples of Bad Weld
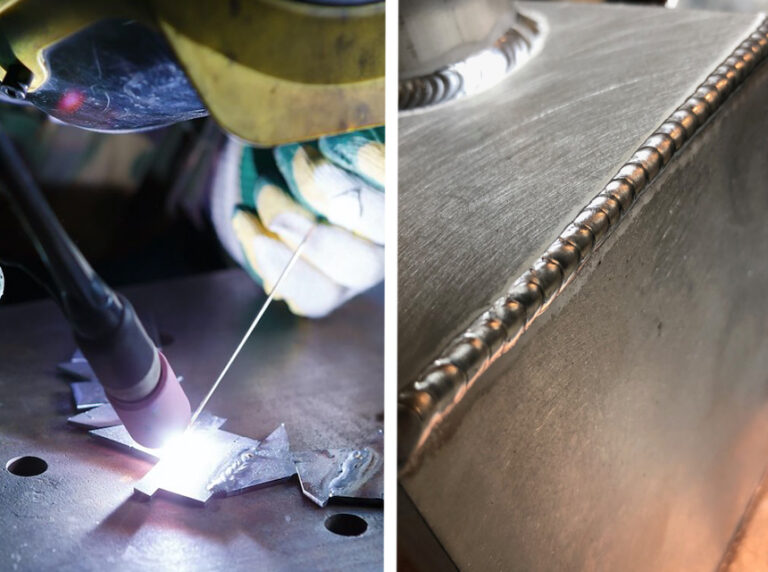
Good Weld vs Bad Weld 4 Methods for Proper Results and Testing Advice
A bad weld can compromise the strength and integrity of a structure, while a good weld can make it stronger. So, how do you know if you're looking at a Bad Weld Vs Good Weld? In this blog post, we will discuss the differences between bad welds and good welds, and teach you how to spot them both! What is a good weld?

How to Spot a Bad Weld Vs Good Weld? (Updated July 2022)
Good Weld vs Bad Weld: Explaining Various Techniques for Consistent Results With this article, you'll learn how to see good weld vs bad weld in various techniques and receive weld testing tips By Christopher McDonagh Reviewed By Thomas Garcia Last updated: August 27, 2023 Weld Zone is reader-supported.

Good Weld vs Bad Weld 4 Methods for Proper Results and Testing Advice
Common Factors of a Good Weld vs Bad Weld Different welding processes produce a wide range of welds. With such variety in the welds, there aren't hard and fast rules for telling apart good and bad welds across the board. Instead, we'll have to look at each type of welding individually.
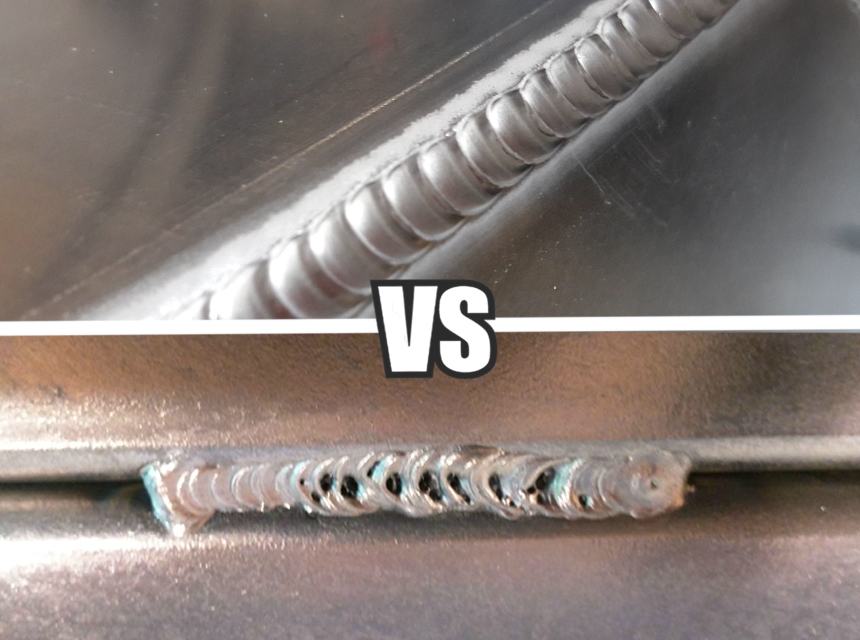
Good Weld vs Bad Weld 4 Methods for Proper Results and Testing Advice
Good TIG Weld Signs A good TIG weld will always seem neat and smooth. If you weld small layered to create a pattern in the weld and if your weld doesn't have any dust powder or burnout it should be considered very good welding vs bad welding. Bad TIG Weld Signs

Good Welds vs Bad Welds How does a good weld look like? Weldingmania
A bad weld can weaken the overall structure and increase the risk of failure, which can be dangerous in certain situations. On the other hand, a good weld ensures that the structure is strong and secure, withstanding the test of time and external forces. So, what exactly distinguishes a good weld from a bad weld?
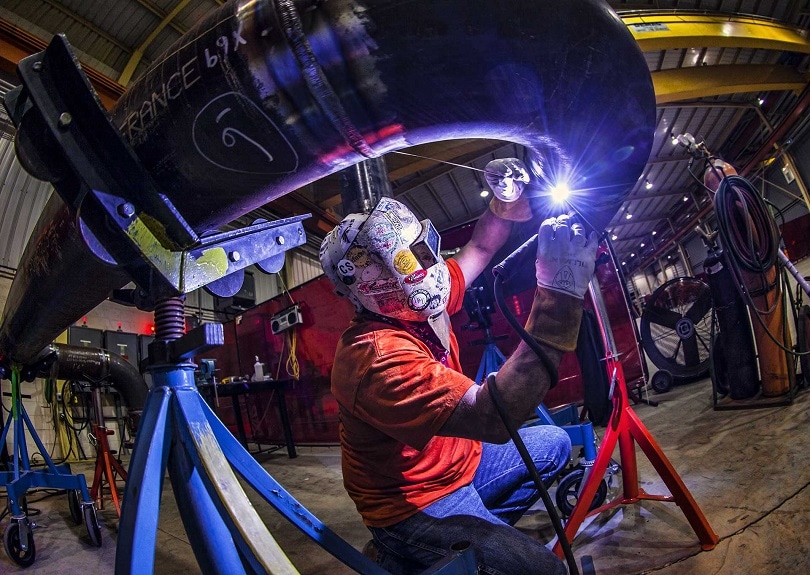
How to Identify a Good Weld vs Bad Weld (with Pictures) WaterWelders
Welding techniques and settings are typically the primary sources of bad weld, which can be countered by improving a welding operator's techniques, set-ups, and knowledge base. Welding operators can take steps to avoid bad welds and produce good welds by adopting the best practices and techniques. This means not only selecting the correct welding process and settings, but also ensuring that.